Machines a wide range of hardened materials
Real tool cost reductions by replacing CBN
BN72: Ideal for hardened materials from 30 – 62 HRC
BC42: Ideal for hardened materials from 55 – 70 HRC
Features
- High hot hardness and low plasticity at high temperature ranges make them ideal for finishing of hardened materials
- Significant tool cost reductions are achieved by replacing CBN
- Inserts with a wiper flat or a chipbreaker are available to further improve machining efficiency
- BN72 excellent for machining carburized or induction hardened steels.
Grade & Speed recommendation chart
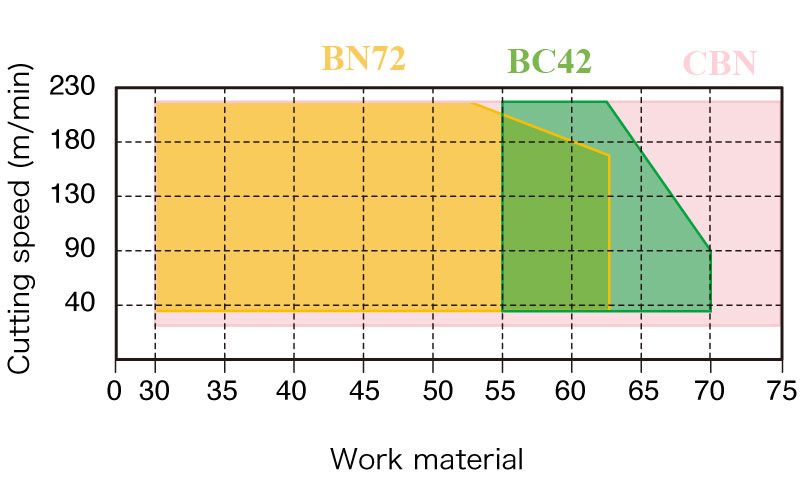
Tooling application
- Hardened material
- Continuous finish turning hardened materials 30-70HRC
Cutting conditions
Grade | Material | Operation type | Machining | Cutting speed (m/min) | Feed(mm/rev) | DOC(mm) | DRY | WET |
BN72 | Hardened material (HRC30-62) | Turning | Finishing | 40 – 200 | – | – | – | – |
BC42 | Hardened material (HRC55-70) |
Recommended Depth of cut and Feed Rate
Corner R | DOC (㎜) | Feed (㎜ /rev) |
---|---|---|
R0.4 | 0.15 | 0.05 ~ 0.08 |
R0.8 | 0.3 | 0.08 ~ 0.10 |
R1.2 | 0.4 | 0.10 ~ 0.13 |
R1.6 | 0.5 | 0.13 ~ 0.16 |
Round Insert | 2.0 | 0.16 ~ 0.25 |
Grade Application Map
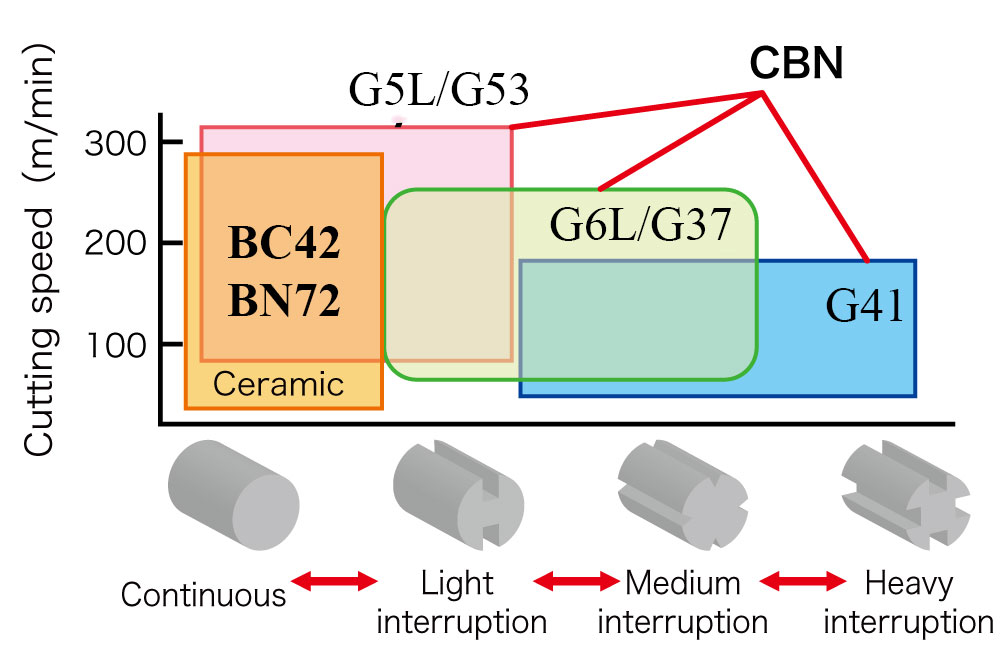
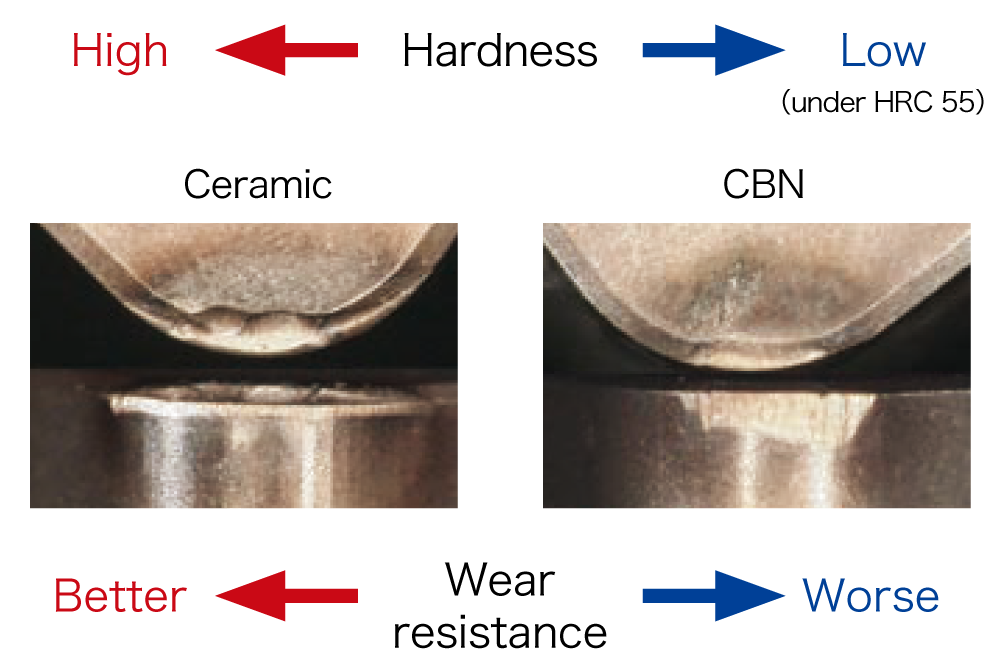

Inserts with a wiper flat or a chipbreaker are available
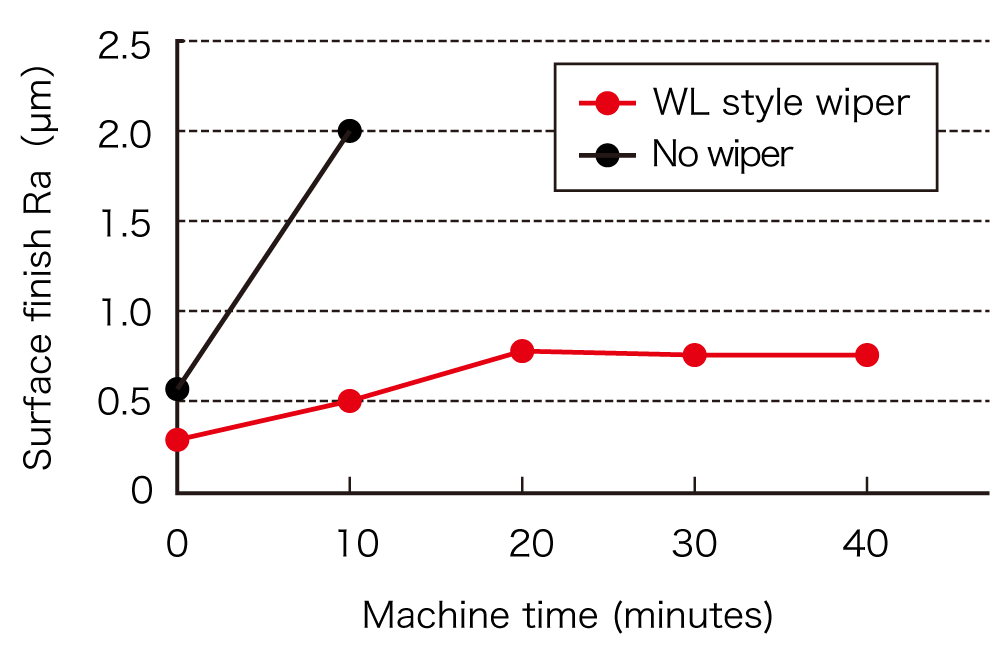
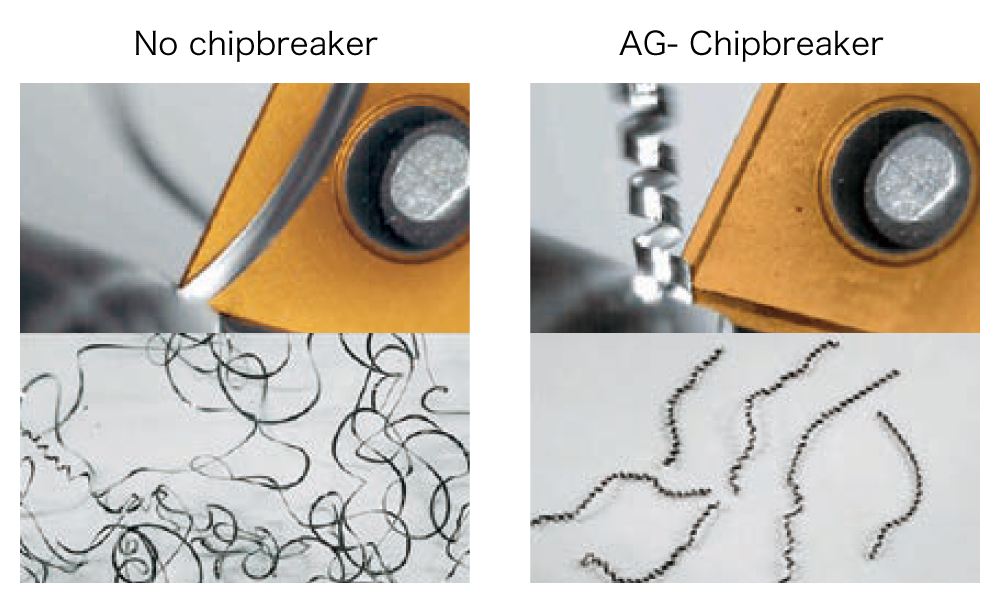
Case Study
Gear | ||
---|---|---|
| ![]() | |
| ||
| ||
| ||
BN72 ( 4 corner ) | 70 pcs / corner | |
Competitor’ CBN ( 2 corner ) | 50 pcs / corner |
BN72 achieved longer tool life per corner and significantly reduced tool costs with 4 corners compared to the competitor’s 2 corner CBN.
Industrial part | ||
---|---|---|
| ![]() | |
| ||
| ||
| ||
BN72 | 50pc/month – stable machining | |
Competitor’ CBN | 50 pcs/month – unstable machining |
BN72 machined the same number of parts as the competitor’s CBN.
BN72 performance was much more stable and significantly reduced tool costs for the customer.