CBN grades ideal for high-precision machining
Roughing to finishing continuous cut operations
Ideal for hardened materials of HRC 55 or higher
Features
- Excellent wear resistance due to optimum CBN content and special TiC binders
- Continuous to light interrupted machining
- G5L- coated CBN grade:
Ideal for machining the hardened material layer and the inner lower hardened layer. A special hard TiCN layer prevents a chemical reaction between the CBN and the iron in the work piece during material removal.
G53 – uncoated CBN grade:
Ideal for machining the hardened material layer.

Tooling application
Continuous operations for hardened material at HRC55 or above
Cutting conditions
⚫ 1st Recommendation ⚪ 2nd Recommendation
Grade | Material | Operation type | Machining | Cutting speed (m/min) | Feed (mm/rev) | DOC (mm) | DRY | WET |
G5L/G53 | Hardened material (HRC55 or above) | Turning Continuous machining | 2290 | 100 – 300 | ~ 0.2 | 0.1 – 1.0 | ⚪ | ⚫ |
Edge preparations

Performance comparison by edge preparation
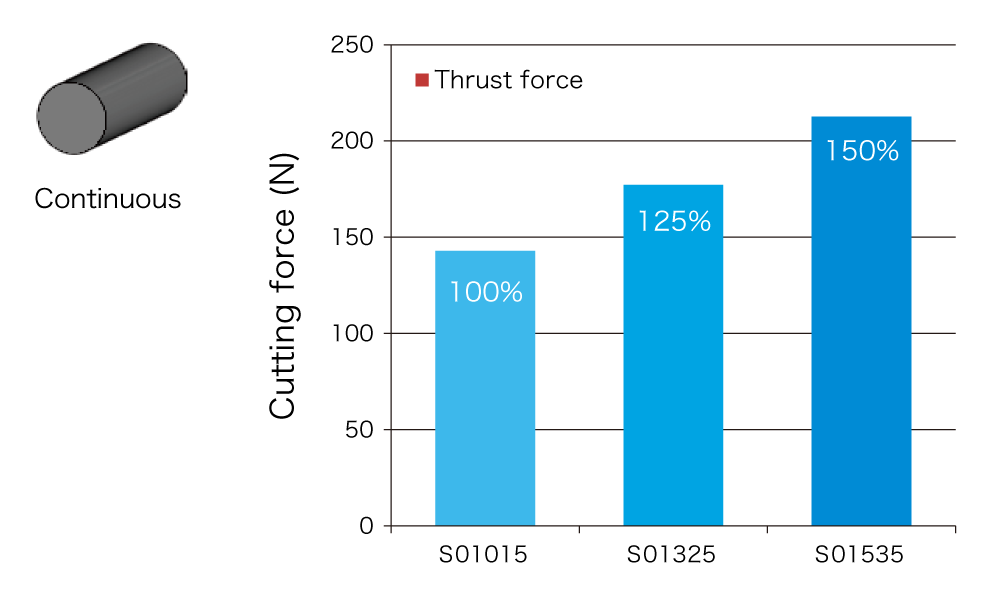
- As the edge preparation increases the tool pressure on the insert increases.
- [ Cutting conditions ] SCM415(HRC63-65) vc=200m/min f=0.1mm/rev ap=0.2mm, DRY
- [ Insert ] TNGA160408
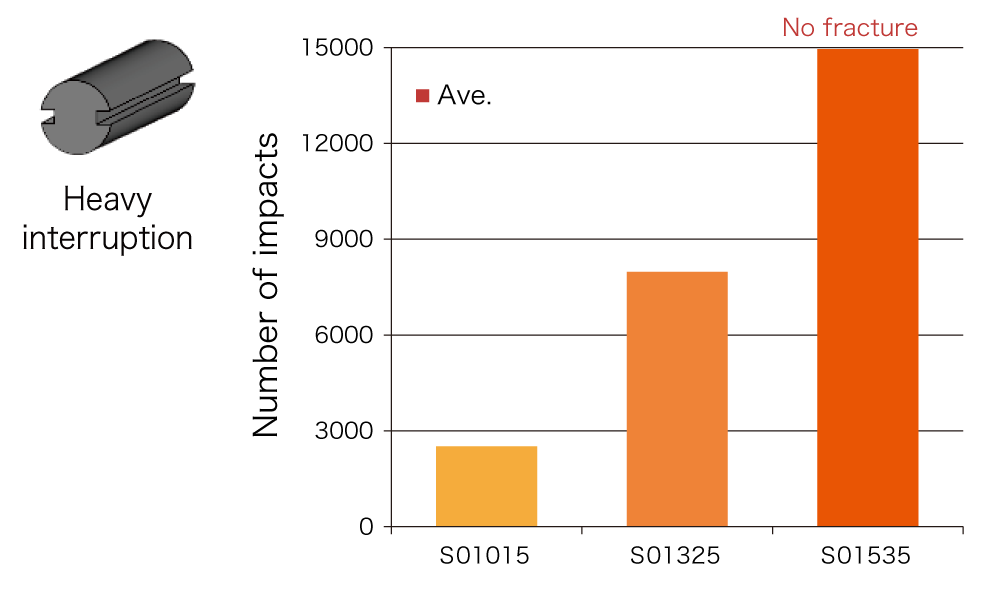
- There is a direct correlation between an increase in the edge preparation and improvement of insert fracture resistance.
- [ Cutting conditions ]
- SCM415(HRC63-65) vc=75m/min f=0.1mm/rev ap=0.3mm DRY
- [ Insert ] TNGA160408
Case study
OD Turning of shaft parts | ||
---|---|---|
| ![]() | |
| ||
| ||
| ||
| ||
G5L | 6 pcs / corner | |
Competitor’s coated CBN | 3 pcs / corner |
G5L achieved 2 times longer tool life.
Due to dimensional changes and deterioration of the machined surface the competitor’s coated CBN needed to be changed.
ID boing of automotive parts | ||
---|---|---|
| ![]() | |
| ||
| ||
| ||
| ||
G53 | 240 pcs / corner | |
Competitor’s coated CBN | 200 pcs / corner |
G53 insert achieved 1.2 times higher tool life than the competitor’s coated CBN insert.